Messick's 60,000 sqft Service Shop New Mt Joy Shop Tour
Tags : new | service | shop | tour |
Messick's 60,000 sqft Service Shop New Mt Joy Shop Tour
Neil from Messick's, here to take you in a tour of the 60,000 square foot shop here at our new Mount Joy store. Messick's has always invested heavily in the parts and service side of the business. We can sell you all the shiny new equipment that's out there, but if we're not taking care of people properly throughout the long ownership experience that you'll have with a whole lot of this equipment, your satisfaction with that machine is not going to be great. This is always a side of the business we've invested heavily in. You may have seen that some years ago. We actually did a previous video on our 40,000 square foot shop, which is massive in and of itself, but moving into the new Mount Joy store here, we needed more capacity to continue to grow our service department and capabilities. So I'm going to take you for a quick walk here this morning. We're going to talk through some of the front side and the back side of what happens in the service department.
Service Lobby
Now we're going to get to the shop here shortly, but this is the side of the service department that you most likely are going to see when you walk in the front door. We use a very automotive based service model with service writers and service managers and this is the customer facing side. It's a bunch of nice improvements we've been able to make here. These folks are now out here in the showroom rather than being up in a building far away and are really close to their service manager. So we get a lot better inter departmental communication. The rental desk is also part of our service department too. They're also down here now in the showroom as well. So it's bringing all of these people together. They're kind of boring though and I think you probably want to see some actual wrench turning. So come with me.
Shop Layout | Four Departments
Now, as we walk out here into the shop, it probably helps to understand what this looks like from the outside a little bit. Each one of these shop areas is actually broken up into four separate shops. So you're going to have a large garage door here on the outside of the building that leads into several bays then to the left and to the right. So there's actually four shops here operating under one giant roof. Just outside those big garage doors is the staging area for all the equipment going in. You can imagine with this many technicians working in one space, there's a constant flow of machinery going in and out of the shop. So outside of these doors is the staging area for the machines going in. When machines come back out again, there's another area that they're going to sit in and then for new equipment that's headed out, there's a separate area on the back over here where things can be good and spread out so that they're easy to get to for pickup.
48 Service Tech Bays
So this is it. It's the new 60,000 square feet service building. Now in here, we have room for 49 service technicians and within each of those bays, there's a whole bunch of new capabilities that the techs have. Now, we had a big facility before, but we had room for 32 technicians in there. That building had been full for a long time. So we hadn't really had the capacity to be able to continue to grow our service department and keep up with a lot of the demands for many of you. Within each bay here, some of the things for the technicians have changed. Walk over here and look at some of the workspaces.
We work on all kinds of different equipment here at Messick's. Everything from small tractors and lawn equipment, Zero Turn mowers, push mowers, up to the biggest combines and self propelled sprayers that you're going to see running around out in the field. Each one of these different pieces of equipment has its own unique challenges and so people who work in different parts of this shop have bays that are set up a little bit differently to help work on that specific kind of equipment.
Higher Ceilings & Chain Hoists
When you look here at the large machinery, there's a couple of different changes here that have been made in this building. For one, the ceiling height has gone up. Seems like every time you pull one of these pieces of equipment in, they seem to be getting bigger and bigger all the time and to be able to do something like lift an engine out of the back of the sprayer, if we're needing to do that, or pull a tank off, we have a chain hoist now that runs over top of the machine. So every technician bay here has a big beam with a hoist that runs over top of it to be able to lift and pull. Now that chain hoist is a couple feet higher than what it's been in our previous buildings and that's because you just need even more of that clearance to be able to work above the machine. So the ceiling height here has gone up.
You'll notice the orange hoses up there. They are all exhaust lines so that we can run equipment indoors. You pull that down and stick it over top of the muffler and fire piece of equipment up in here. Also up on the ceiling are big fans. The building in here is not air conditioned, but it has these big fans up here to circulate the air. We've put those into many of our shops now. Even though these spaces, aren't air conditioned, keeping that going makes it very tolerable to work out here, even on a hot day.
Indoor Truck Parking
You'll notice this big space here in front of me. That's a parking space for a service truck. So previously many of our trucks had to be parked outside. Service trucks are huge investments. A fully stocked service truck, not counting the technician's tools and investments, can cost the dealership here over a hundred thousand dollars. That's the cranes, the generators, the welders, the truck body, the truck itself. They're serious investments. Being able to park those things inside has a bunch of benefits.
One, it keeps the truck clean. It's going to last longer because it's not out in the weather, but it's also a big bump to our efficiency, right? We're always looking at keeping our technicians as productive as possible to make sure you're getting as much value from every hour of work that they put into your piece of equipment. If their tools are in their truck, way out in a parking lot over here, and they've got to go get a wrench, walking back and forth is not a good use of their time. So this arrangement here in this building now actually has parking spaces inside of the shop so all the things that they might need to work on your piece of equipment are right beside them.
Typical Technician Workstation
This is a typical technician workstation. So you have a big steel work bench to be able to spread your stuff out on while you're working. You can have electrical outlets back here against the wall to plug things in. LED lighting over top of them so you have a bright place to be able to work. Each one of these hose reels here is going to give you a hose reel for electric, a hose reel for air, to be able to pull out if you're working on things. You'll notice some people up here have a third one too, are going to have a light if they need to pull a light out to work underneath of something.
Every station here also has some technology that comes along with it. About half of our technicians work on the road and are going to have laptops. The other half have desktop computers here. You're going to have a place to sit down and plug in. So we write a lot of our own service departments scheduling, planning, and job software. It's one of the things that we're proud of here at Messick's, are our investment in all of these processes. So all of your work typically comes across your computer station here. Now, if you need parts, you'll order all of your parts from that computer station and they're brought out to you from the parts department within a couple of minutes. It's a process that we really try to keep moving along. Each one of these stations also has a telephone. Because we've got some distance here between the space here in the shop and where a service manager may be, there's an easy telephone here to pick up and call somebody if you need help, rather than hiking across the building.
Shared Resources
It's a little hard to picture exactly how this large building is laid out, but essentially there's four different shop areas here across the building and then the central area here that sits in the middle that's the shared resources. So what we're looking at here is all the things that are shared across these shops. This large pallet racking has storage for things like engine jigs, battery disposal, tire changers, tire filling, drill presses, parts cleaners. That kind of industrial equipment and tools that are needed to work in these different spaces is all stored here so it's easily available in the middle. We also have storage spaces back here for all the parts and everything that are going to be needed for a job that's about to happen, right? A staging area in order to move things quickly over the technician to start their work.
Clean Room & Weld / Fabrication Rooms
Behind us here, there's two more rooms. Let's walk back here and take a look. We don't do body work here at Messick's, but we do have a clean room in order to, say, do a little bit of painting with some rattle cans or go through and detail a piece of equipment. This clean room space gives us some place to do that. So we have an outside garage door that we can pull a piece of equipment in, in order to have a nice clean space in order to prep things away from all the dirt of the shop. Adjacent to the clean area is a small space here for welding and fabrication. So we're going to have torches, welders, large vices. We've got beams set into the floor if we need to straighten a frame or something. We can pull a frame down against a jack against the floor. We keep steel storage in here. We're not manufacturing implements here per se, but we've got enough facilities to be able to do a significant repair or in many cases, beef up something that may not be holding up appropriately.
Tool Room
One thing you may not realize is the dollar investment that dealerships have in specialty tools. Every time a manufacturer comes out with a new model, if they've got special jigs or tools that are required in order to work on that machine, in most cases, we're required to purchase all of those extremely overpriced expensive tools the moment one of those new machines arrives before a failure has even happened. We have a special room back here that stores all that stuff and a tagging and cataloging system in order to keep track of all of it because of the sheer dollar value that's tied up and all of that stuff. So when you need it, you need it. It's here. We're always going to be able to find it, but we've got a special space back in here to store all of those things.
Locker Room and Wash Stations
Working on equipment can be a dirty job. When you walk around the shop here, you'll find an ample amount of wash sinks, soap on the wall, automatic dispensers for paper towels and things to make it easy to clean up after a dirty job. Part of our goal in making a lot of these investments is to be the best place to come and work if you're working on machinery, right? This is a challenging industry to find the amount of help that we need and our goal here is to attract the best of the best in this business, by providing some of these niceties. Another one of those things is a locker room, right? If you come into work and you're working on a dirty job, you don't want to take that dirt home with you. We have uniform services and locker rooms to be able to come in here and change after a dirty day. There's also a shower upstairs if we need to use that sinks and mirrors and everything over here to kind of clean yourself up before you go out at the end of the day.
Coffee Stations
So totally guilty here, myself, of walking around the building and trying to find what I can find in order to eat every once in a while. One of my favorite things here in being able to come into a new building like this is that we have about a half a dozen different places set up around the building for coffee, right? As big as this building is you need multiple coffee stations. You can't just have one pot that everybody goes and uses. There's water dispensers, coffee station, place for everybody to put their shared cookies out. Microwave if you need to heat something up, and a sink again, to have a cleaner space over here. If you're say washing up your lunch, you're not doing it in a shop sink. So stations like this are actually replicated in a number of different places around the building.
Backend Offices
We talked about the offices up on the front side of the business. There's a couple back here in the shop as well. Those are for the department within the shop here that handles all the setup of new equipment. That service manager is located back here, right next to his technicians. There's also an office back here for the trucking dispatcher, because that tends to be a a back of the business type role. That office is shared in the back here and they work side by side with that setup department, in order to get new equipment delivered out to our customers.
Room for Growth
You notice the amount of open space that's in these bays. There's a reason for some of it, right? There's space in here for those parking spaces, working on bigger and bigger equipment all the time, we need the space, but there's two other things going on here too. This side of the building can't ever get any bigger. This is the biggest this building is ever going to be able to be. We've got future plans. If we happen to outgrow other areas here of what we've built, there's expansion possibilities, but the shop is never going to be able to house more than the 49 mechanics that we've planned for. So this is a little overbuilt over here to give our space some of that room for future growth.
More Articles
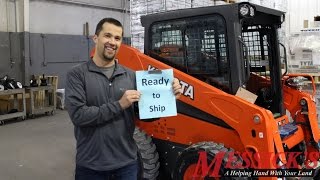
Review of the new Kubota SSV65 Skid Loaders
Here with the very first of our Kubota SSV skid steers. We're really excited to show these to you here today. This is probably for us one of the biggest Kubota product launches we have ever had. The demand and excitement among our customers and our staff here is probably a new record among products that we've had through here before.